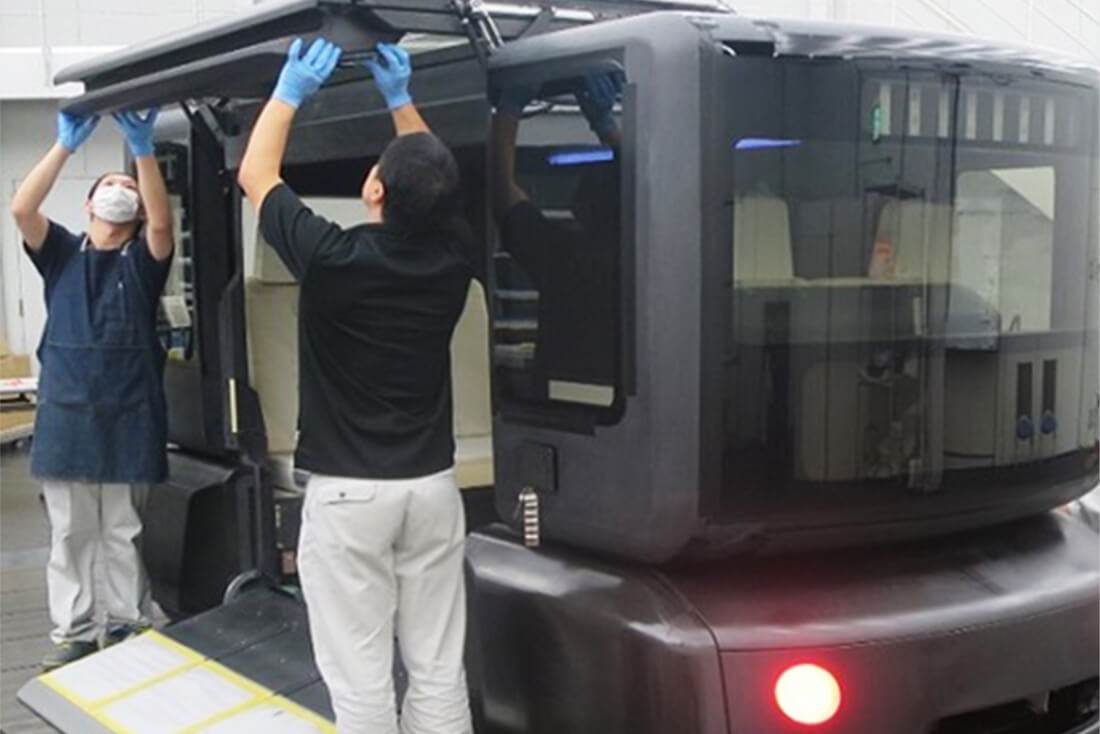
■Issue
初めての成形方法にトライ
難易度が高く、工期も短い(約4ヶ月)ため、各工程の主担当者を選任し、フォーメションを組んで対応しました。
イベントでは、一般の来場者を乗せて前方と後方に無人運転をする演出を行うため、過去に例をみないほどの安全性・耐久性を考慮した物作りが課題となりました。特に、電動で開閉するドアは、上側は跳ね上げ式・下側はスロープ式というデザインでしたが、車輌のドア開口部ほどの厚みの中に機構部品やモーターを収める設計には、たいへん苦労しました。
さらに、パワーユニットはお客様から支給されるモーターの条件を満たすため、人が乗らない状態で1600kgを超えないという重量制限の目標値を立て、設計に取り組みました。
また、キャビンやドアパネル、外装パネルは、レース車輌に多用されるドライカーボンという成形方法を採用しましたが、私たちにとってこれを多用するのは、今回の案件が初めてでした。それでも、キャビンの前後部分にはドライカーボンをモノコック構造で製造することにこだわり、1400kg弱の重量に収めることに成功しました。
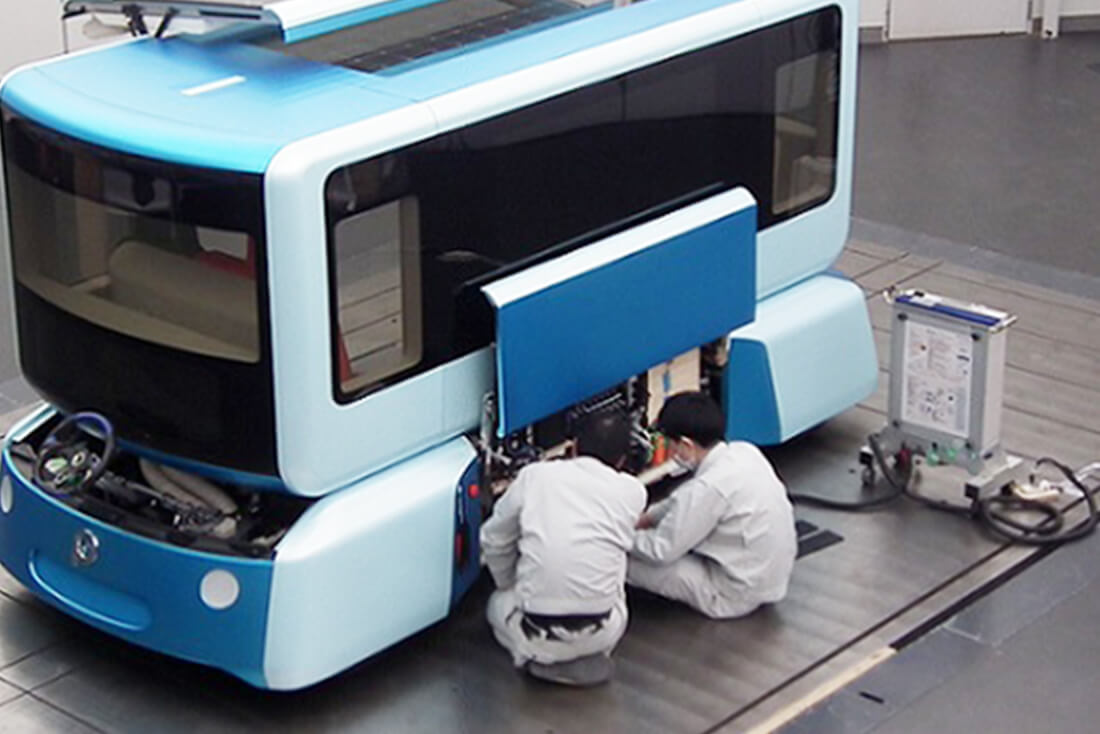
■Resolution
期待を超えたドアの開閉機構
設計工程では、お客様と仕様について綿密なやり取りを行いながら進めました。
製造工程のスタート前に設計を完了させなければならない責任と、協力先に依頼したドライカーボンモノコックキャビンが設計どおりでき上がるのかという不安から、緊張感に満ちた日々が続きました。
それでも、営業、プロジェクトリーダー、生産管理、各生産部門の担当の役割を明確にし、各人が能動的に仕事に取り組んだ結果、シートをお客様のコンテンツに合わせて電動で動くように製造した点も功を奏し、難易度が高い案件にもかかわらず、お客様の要求を満たすコミューターが完成しました。
また、苦労したドアに関しては、納品後もメンテナンスが必要になる場面はあったものの、制約の多い条件下での開閉機構を実現させたことおよび高い安全性を盛り込めた点については、お客様にたいへん喜んでいただいたのではないかと考えています。